Posadzki przemysłowe cz.2
Podczas użytkowania posadzki ujawniają się uszkodzenia wierzchniej warstwy wykończenia, będące skutkami nie tylko błędnego wykonania, ale i braku wyspecyfikowania części parametrów na etapie projektowania.
Najczęstsze uszkodzenia
Warto poznać, jakie błędy wykonawcze w zakresie posadzek przemysłowych utwardzanych powierzchniowo występują najczęściej.
Pylenie, nadmierne ścieranie (fot. 1]
Czynnikami wpływającymi na nadmierne pylenie i ścieranie są: nierównomierne rozprowadzenie warstwy utwardzającej lub zbyt mała ilość dozowanego materiału posypki. Powodem problemów może być również utrudniony proces wnikania posypki w strukturę betonu będący skutkiem zbyt późnego jej zacierania oraz niewłaściwy lub całkowicie pominięty proces pielęgnacji wykonanej posadzki.
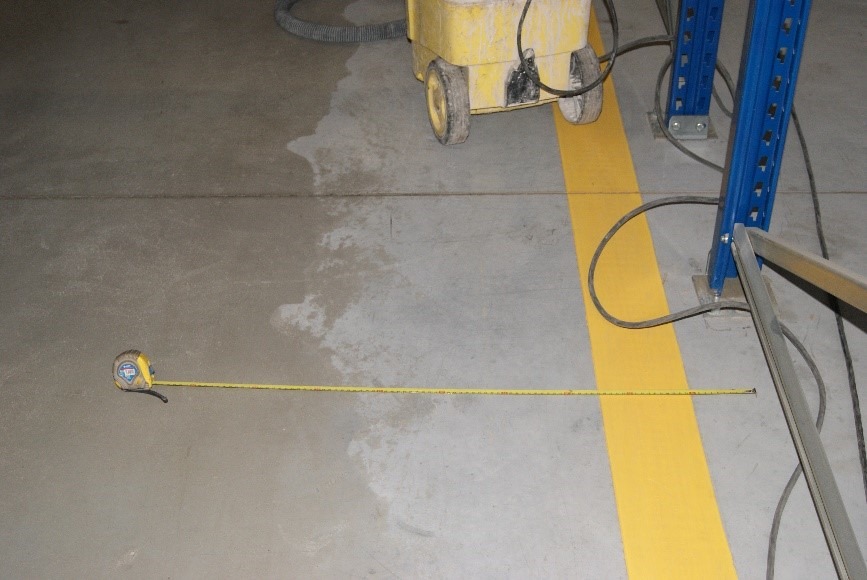
Zarysowania i pęknięcia (fot. 2]
Przyczyn występowania zarysować i pęknięć posadzki jest bardzo wiele. Defekty tego typu psują jej estetykę i związane są bezpośrednio z funkcjonalnością i trwałością. Rysy najczęściej występują ze względu na naprężenia skurczowe betonu we wczesnej fazie układania posadzki. Jest to związane często z nieodpowiednią jej pielęgnacją, wykonaniem zbyt płytkich lub w nieodpowiednim terminie nacięć dylatacyjnych lub całkowitego ich braku. Dodatkowo dochodzą zjawiska związane z osiadaniem podłoża pod wykonaną posadzką lub nadmiernym obciążeniem konstrukcji nośnej posadzki.

Siatka mikrospękań i mikrozarysowań [fot. 3]
Najczęściej powstanie mikrorys powodowane jest przesuszeniem posadzki, zbyt dużą ilością posypki lub innymi czynnikami technologicznymi podczas zacierania i utwardzania posadzki.

Odpryski spowodowane korozją mrozową kruszywa [fot. 4]
Odpryski tego typu najczęściej wynikają z niewłaściwego doboru kruszywa w recepturze mieszanki betonowej lub niskiej jakości kruszywa posypki w odniesieniu do panujących warunków klimatycznych. Są to defekty ściśle związane z brakiem odporności ziaren kruszywa do przenoszenia zmian objętości wywołanych niestałymi warunkami fizycznymi, takimi jak zamrażanie-odmrażanie lub naprzemienne nawilżanie i suszenie. Uszkodzenia tego typu dość często są spotykane na parkingach garażów wielopoziomowych (np. w centrach handlowych], które mają zadaszenia, ale ze względu na jeżdżące samochody oraz mycie są stale zawilgacane.
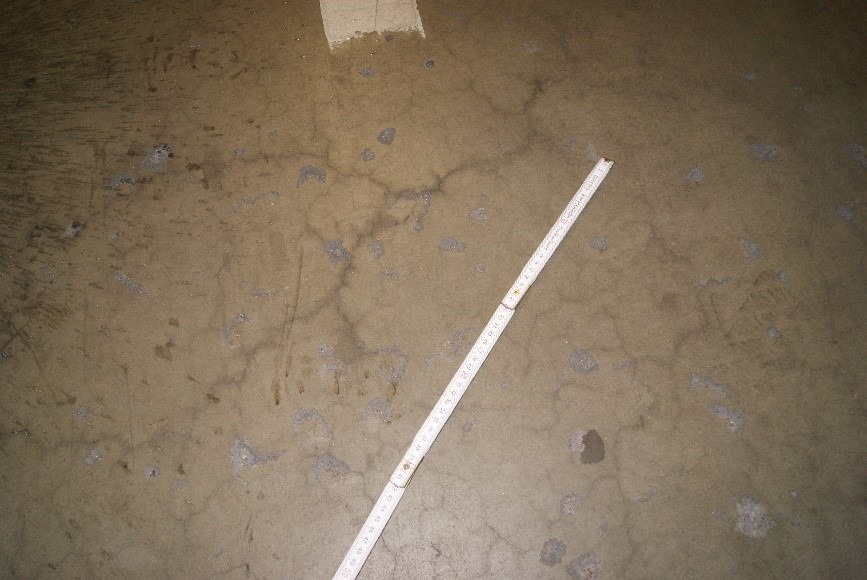
Odpryski spowodowane reakcją alkaliczną kruszywa betonu płyty z cementem [fot. 5]
Uszkodzenia są wynikiem szkodliwych reakcji aktywnej krzemionki pochodzącej z kruszywa z alkaliami zawartymi w cemencie. Reaktywnymi alkalicznie kruszywami najczęściej są ziarna porowatych wapieni, gezy [zawierającej bezpostaciową krzemionkę), krzemienie, chalcedon, rogowce, trydymit, czerty oraz lidyty. Reakcje reaktywnej krzemionki z alkaliami cementu rozpoczynają się od agresji wodorotlenków pochodzących z alkaliów cementu na minerały krzemionkowe z kruszywa. Tworzy się wówczas żel alkaliczno-krzemionkowy, będący związkiem mogącym wchłaniać duże ilości wody, zwiększając tym samym swoją objętość, Powstały pęczniejący produkt powoduje wewnętrzne ciśnienie, w wyniku którego dochodzi do spękań, rozpadu i zniszczenia otaczającego uwodnionego zaczynu cementowego, Procesy te zachodzą tylko z udziałem wody. Minimalna wilgotność względna we wnętrzu betonu umożliwiająca zajście wymienionych reakcji wynosi ok. 85% przy temperaturze 20°C, Badania wykazały, że reakcje alkalia – krzemionka najszybciej zachodzą w zakresie temperatur 10-36°C. Intensywność tego typu reakcji w dużym stopniu zależy od wielkości ziaren oraz ich porowatości. Jeżeli źródłem alkaliów jest tylko cement, to ich koncentracja zależna będzie od wielkości reaktywnej powierzchni ziarna kruszywa. Destrukcja posadzki objawia się w postaci kraterów o głębokości nawet do 3 cm, w formie tzw. pop-outów. Występowanie kruszyw reaktywnych alkalicznych w betonie powoduje jednak duże uszkodzenia powierzchni i ma zdecydowanie większy wpływ na obniżenie trwałości powierzchni. Jedynym sposobem zatrzymania reakcji alkalia – krzemionka jest wysuszenie betonu oraz jego odcięcie przed dostępem wilgoci.
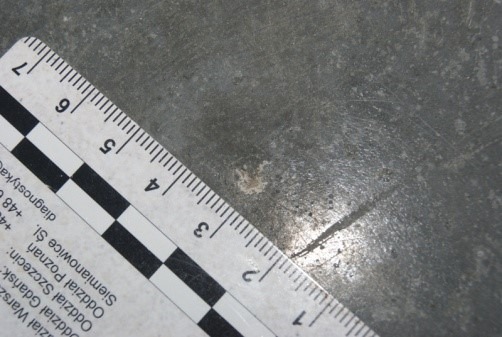
Odpryski spowodowane reakcją alkaliczną kruszywa posypki z cementem [fot. 6]
Podobnie jak ma to miejsce w przypadku reakcji alkalicznych kruszywa betonu płyty konstrukcyjnej z cementem, zastosowanie kruszywa reaktywnego alkalicznie (ziarna kruszywa AAR zarówno krzemionkowych ASR, jak i węglanowych ACR) w posypce również może powodować reakcje z alkaliami cementu. Osłabienia przyczepności ziaren kruszywa z uwodnionym zaczynem cementowym powoduje stopniowe wykruszanie się pojedynczych ziaren z powierzchni użytkowanej posadzki.
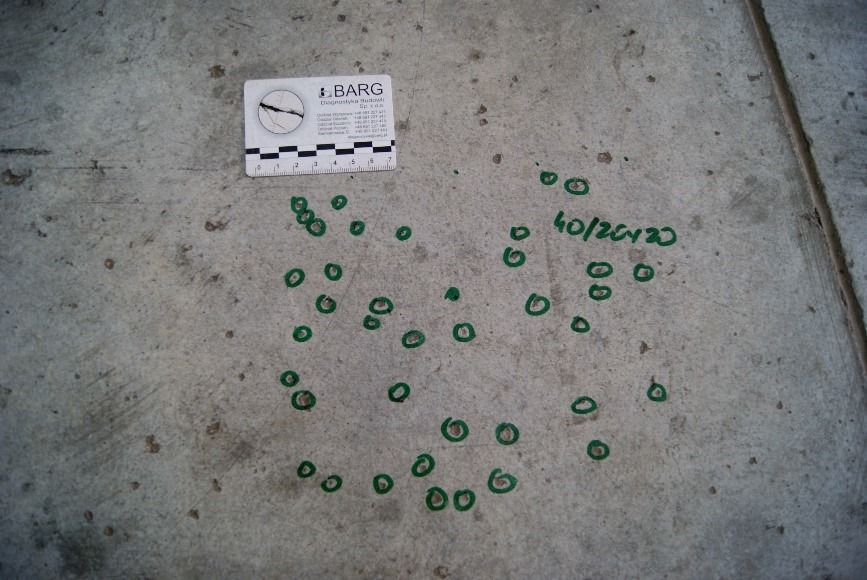
Wykruszanie się ziaren posypki
Schemat powstawania odprysków w posadzce jest związany z wystawaniem części ziarna ponad powierzchnię posadzki i jego obluzowywaniem się pod wpływem tarcia ruchu użytkowego [kołowy, pieszy]. Ziarno, które jest cyklicznie poruszane, obluzowuje się i odpryskuje z posadzki. Mechanizm ten jest ściśle związany z brakiem odpowiedniego zamocowania ziaren przeważnie drobnego kruszywa.
Wystające włókna zbrojenia rozproszonego na powierzchni [fot. 7)
Zwiększona ilość wydostających się włókien stalowych zbrojenia rozproszonego z płyty posadzkowej może mieć wiele przyczyn. Jednym z głównych powodów jest nadmierne zacieranie. Częstym powodem defektów jest również zjawisko tzw. bleedingu [wyrzucanie wody na powierzchnię betonu) podczas wykonywania płyty konstrukcyjnej, przez co formowanie i zacieranie posadzki jest utrudnione. Zwiększona ilość wody w warstwie przypowierzchniowej posadzki powoduje lokalne osłabienie struktury betonu, obniżając jej powierzchniową wytrzymałość oraz trwałość przez jej nadmierne wycieranie podczas eksploatacji.
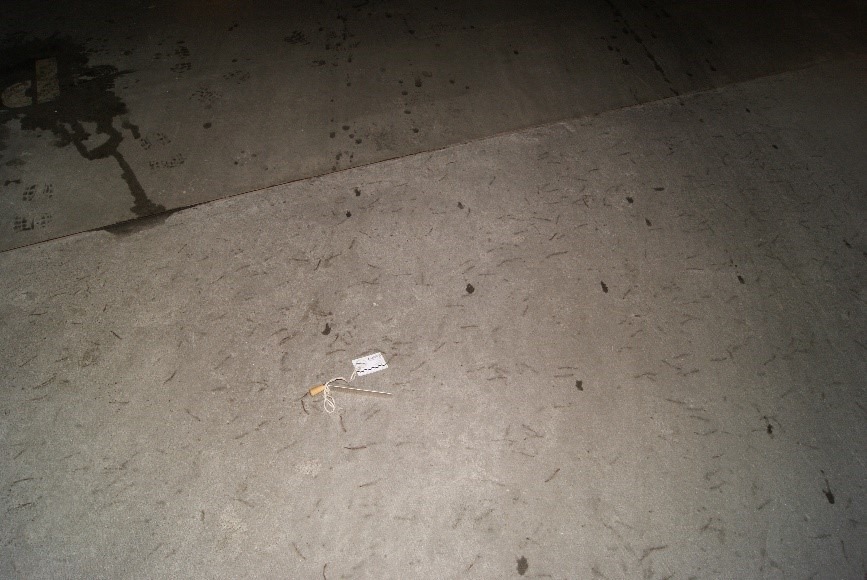
Zdegradowana powierzchnia betonu spowodowana korozję mrozową [fot. 8)
Silna korozja mrozowa lub korozja mrozowa wywołana obecnością soli odladzających na całej powierzchni posadzki występuje najczęściej w przypadku posadzek narażonych na bezpośrednie działanie czynników atmosferycznych, czyli zlokalizowanych na zewnątrz, na terenie nieosłoniętym. Jest to spowodowane zwykle niedostosowaniem parametrów betonu do panujących warunków środowiskowych i wykonanie płyty konstrukcyjnej z betonu nieodpornego na działanie mrozu w obecności soli odladzających.

Uszkodzenia powierzchni na skutek korozji kwasowej [fot. 9)
W zakładach przemysłowych produkcji spożywczej można bardzo często zaobserwować zjawiska korozji kwasowej wynikające najczęściej z rozkładu węglanu wapnia przez kwasy i erozję ługującą wskutek oddziaływania urządzeń myjących. Powierzchnie mineralne w odróżnieniu od żywicznych są nasiąkliwe. Poddane działaniu środków chemicznych nie stanowią w pełni zabezpieczenia przed agresywnym środowiskiem chemicznym.
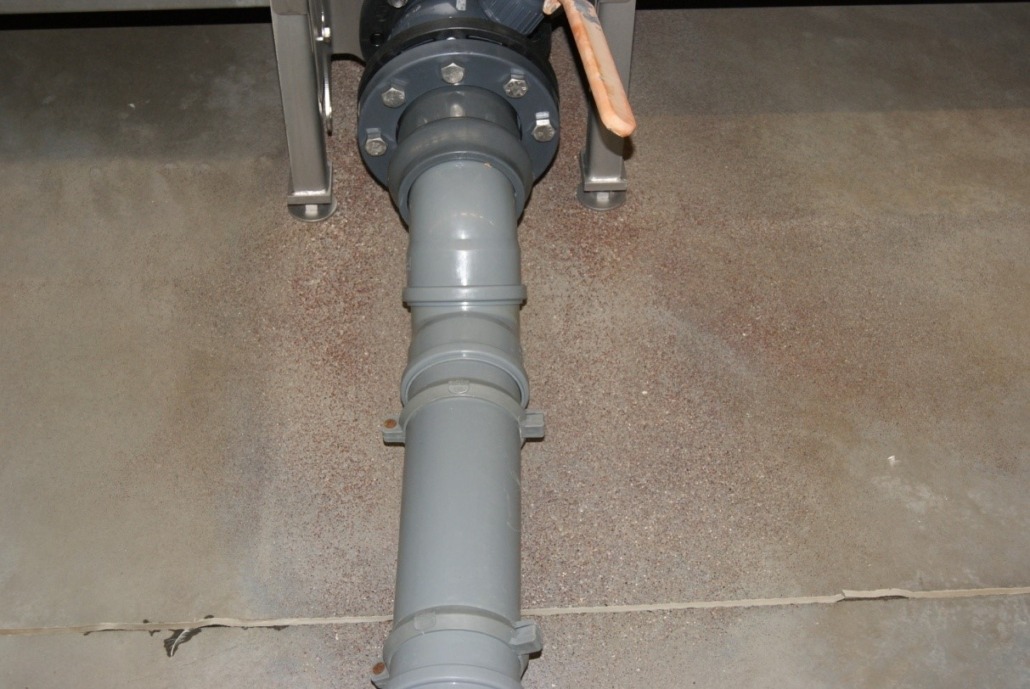
Odparzenia wierzchniej warstwy posypki (delaminacje) [fot. 10)
Wykonywanie posadzek przemysłowych w skrajnych warunkach pogodowych przysparza bardzo często wielu problemów z odparzaniem się warstwy wierzchniej. Mówimy wówczas o występowaniu delaminacji poziomych. Jest to związane najczęściej ze zbyt późnym lub zbyt wczesnym rozpoczęciem procesu zacierania. Dodatkowo na odparzenia może mieć wpływ zbyt szybka ucieczka wody spowodowana nadmierną temperaturą powietrza, zbyt intensywnym przepływem powietrza oraz niewystarczającą pielęgnacją. Odparzenia posadzki sięgają nawet 2 cm w głąb warstwy wierzchniej.
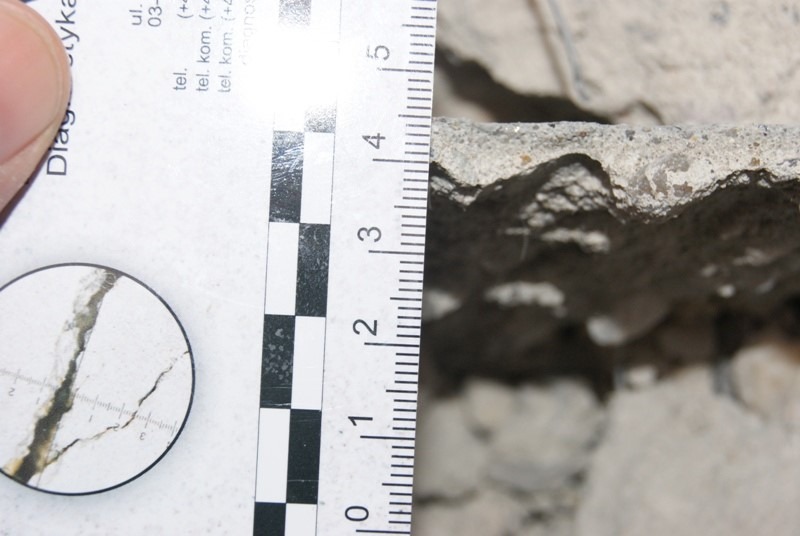
Nadmierna ścieralność [fot. 11]
W przypadku wielkopowierzchniowych magazynów logistyki, zakładów przemysłowych czy stacji kontroli pojazdów, ze względu na silną eksploatację czy duże obciążenie, często w miejscach przejazdów następuje nadmierne wycieranie się materiału utwardzającego. Uszkodzenia mogą występować z powodu doboru posypki utwardzającej o niewystarczających parametrach trwałościowych w stosunku do panujących warunków. Niejednokrotnie są efektem braku właściwej pielęgnacji lub zbyt małej ilości wtartej posypki.
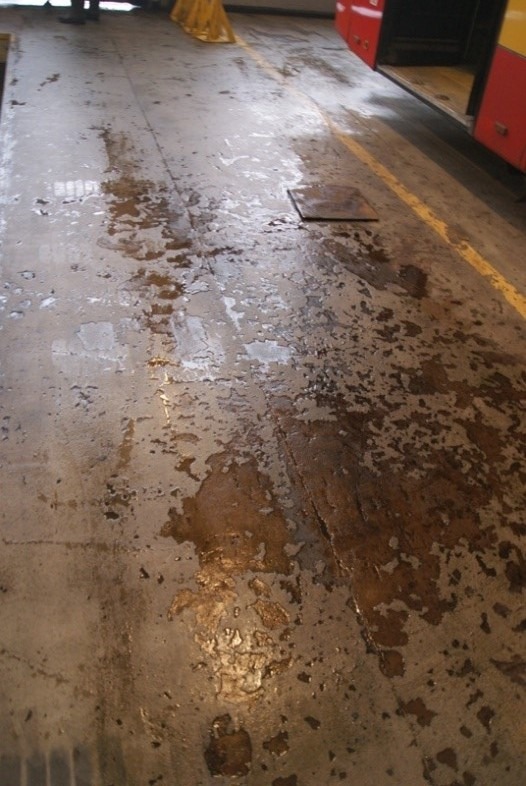
Podsumowanie
Posadzki przemysłowe utwardzane powierzchniowo przez tzw. suche posypki są najpopularniej stosowanym sposobem wykonania warstwy wykończeniowej stosowanej współcześnie w budownictwie usługowym i przemysłowym. Na etapie projektowania bardzo często nie specyfikuje się parametrów fizykochemicznych odnośnie do wymagań stawianych posadzkom. Projektanci opisują najczęściej jedynie parametry wytrzymałościowe betonu pod kątem obciążenia warstwy konstrukcyjnej. W zaleceniach projektowych często brakuje wymagań dotyczących warstwy wierzchniej posadzki lub opisane są one bardzo ogólnikowo. Powyższe braki w projektach są efektem niedostosowania posadzek do rzeczywistych warunków środowiskowych i eksploatacyjnych.
Powszechnie wybierane są najtańsze rozwiązania, nie zawsze zapewniające odpowiednią trwałość i funkcjonalność posadzek. Brak dostosowania posadzek do sposobu użytkowania oraz dodatkowo niezamierzone błędy wykonawcze są powodem częstych napraw posadzek w krótkim okresie od ich wykonania. Dla prawidłowo realizowanej inwestycji projektant wraz z przyszłym użytkownikiem posadzki na etapie projektowania powinni przeprowadzić pełną analizę szczegółowych warunków użytkowania, uwzględniając nie tylko koszty budowy, ale również późniejszą eksploatację.
Opracował:
mgr inż. Karol Sadłowski
mgr inż. Damian Urbanowicz
mgr inż. Maciej Warzocha
- PN-EN 13318:2002 Podkłady podłogowe oraz materiały do ich wykonania. Terminologia.
- AGI 302. 1R-04; ACI Committee 302, Guide for Concrete Floor and Sfab Construction. America Concrete Institute, 2004.
- Bautech Sp. z o.o., Karty techniczne produktów.
- PN-EN 206:2014-04 Beton. Wymagania, właściwości, produkcja i zgodność.
- W. Ryżyński, Utwardzanie powierzchniowe posadzki betonowej, „Inżynier Budownictwa” nr 4/2015.
- B. Chmielewska, G. Adamczewski, Wady i naprawy posadzek przemysłowych utwardzanych powierzchniowo, materiały XXVI Konferencji Naukowo-Technicznej „Awarie budowlane”, 2013.
- H. Rainer Sasse, Wymagania projektowe i użytkowe, Seminarium Naukowo-Techniczne „Podłogi przemysłowe”, 2007.
- A. Szydło, Nawierzchnie drogowe z betonu cementowego, Polski Cement Sp. z o.o., 2004.
- IBDiM, GDDP, Katalog typowych konstrukcji nawierzchni sztywnych. Warszawa 2001.
- DIN 18202 Toleranzen im Hochbau – Bauwerke Tabelle 3.
- PN-EN 12620+A1:2010 Kruszywa do betonu.