Industrial Floorings Part 2
As the flooring is used, the damage to the top layer of the finish is revealed which is not only the result of being made incorrectly, but is also the result of the missing specification of some parameters at the design stage.
The Most Common Damage
As far as surface hardened industrial floorings are concerned, it is worth to know what errors occur most often at the construction stage.
Dusting, Excessive Abrasion (Photo1]
Factors that affect excessive dusting and abrasion are: uneven distribution of the hardening layer or insufficient amount of dispensed dry-shake material. The reason for the problems may also be the impeded dry-shake process of concrete structure penetration resulting from trowelling that may have been made too late and the process of flooring care that may have been made incorrectly or may not have been made at all.
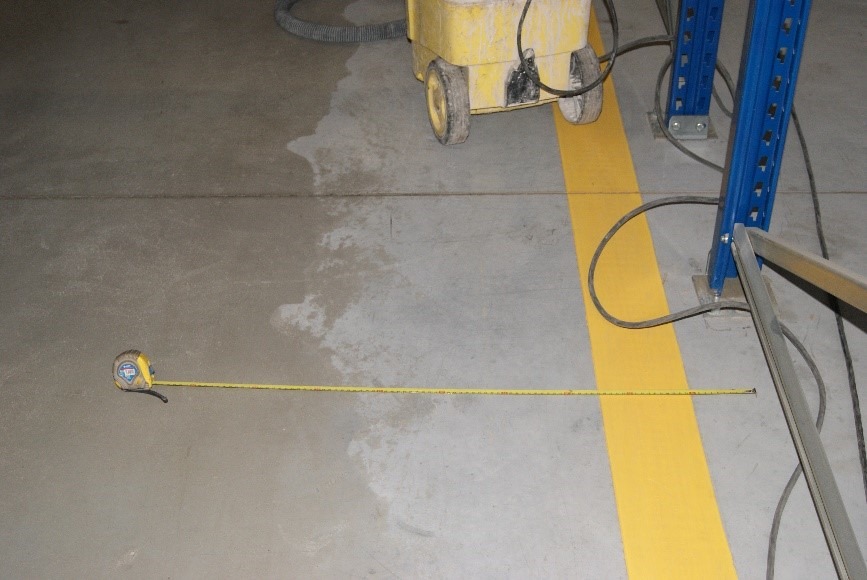
Scratches and Cracks (Photo 2]
There are many reasons for scratches and cracks in the flooring. Defects of this type make its aesthetics deteriorated and are directly related to its functionality and durability. Most often, scratches occur due to concrete shrinkage stresses in the early phase of paving the flooring. This is often because it is inadequately cared for, too shallow dilatation cuts were made at the wrong time or no cuts were made at all. In addition, there are soil settlements phenomena under the flooring or the supporting structure of the flooring is excessively loaded.

Grid Of Micro-Cracks And Micro-Scratches [Photo 3]
Most commonly, micro scratches are caused by excessive flooring drying, too much dry-shake or other technological factors acting during the flooring trowelling and hardening.

Chips Caused by Frost Corrosion of Aggregate [Photo 4]
Most commonly, chips of this type occur because aggregate in the concrete mixture formula were improperly selected or because dry-shake aggregate were low quality in relation to the prevailing climatic conditions. These defects are strictly related to the lack of resistance of aggregate grains to transfer the volume changes caused by unstable physical conditions, such as freezing-thawing or alternate dampening and drying. This type of Damage is quite often found in multi-level garage parking lots (e.g. in shopping centres), which have canopies, but because of moving cars and washing are permanently moistened.
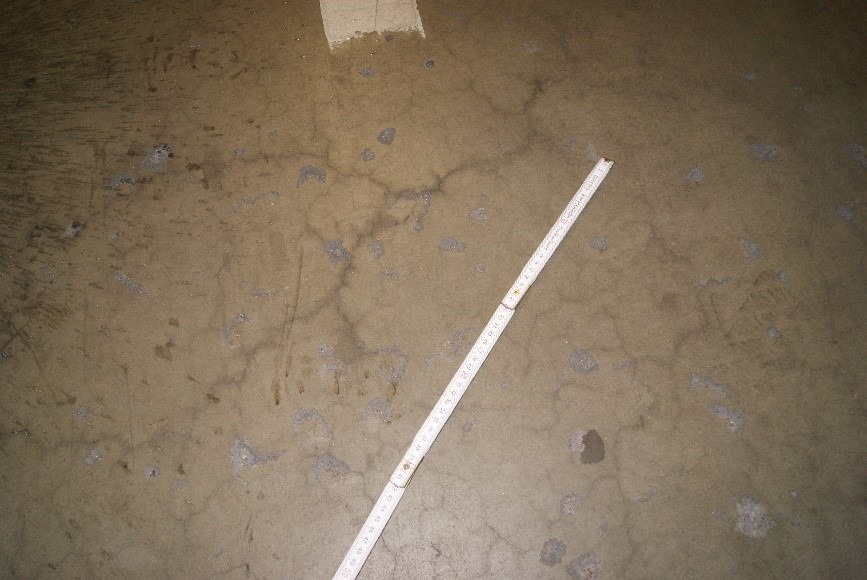
Chips Caused by the Alkaline Reaction of the Concrete Aggregate with Cement [Photo 5]
The damage is the result of the harmful reactions of active silica obtained from the aggregate with alkali contained in the cement. Most commonly, alkali-reactive aggregate are grains of porous limestones, gaizes (containing amorphous silica), flints, chalcedony, hornstones, tridymite, cherts and lidites. The reactions of reactive silica with cement alkali start with the aggression of hydroxides obtained from the alkalis of cement to the silica minerals of the aggregate. An alkaline-silica gel, which is a compound capable of absorbing large amounts of water, is then created, thus increasing its volume. The swelling product obtained causes internal pressure. As a result, cracks are created; the surrounding hydrated cement grout breaks and is destroyed. These processes only occur with water. The minimum relative humidity inside the concrete that lets these reactions happen is approx. 85% at 20°C. The tests have shown that the alkali – silica reaction is the fastest in the temperature range of 10-36°C. The intensity of this type of reaction depends to a large extent on the size of the grains and their porosity. If cement is the only source of alkali, then their concentration will depend on the size of the reactive surface of the aggregate grain. Flooring destruction is manifested as craters of up to 3 cm deep, in the form of so-called pop-outs. However, the occurrence of reactive alkali aggregates in concrete causes large surface damage and has a much greater impact on the reduction of the surface durability. The only way to stop the alkali – silica reaction is to dry the concrete and cut it off from the impact of moisture.
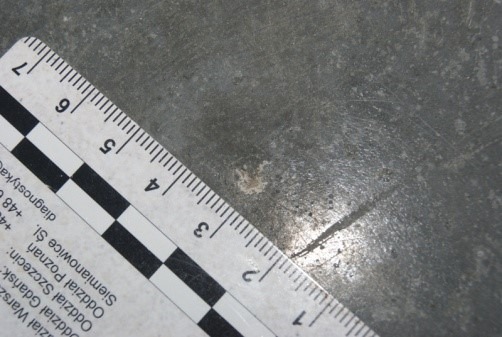
Chips Caused by the Alkaline Reaction of the Dry-Shake Aggregate with Cement [Photo 6]
As it is with the alkaline reactions of the concrete aggregates of a constructional slab with cement, the use of alkaline reactive aggregate (AAR aggregate grains of both ASR silica and ACR carbonate) in the dry-shake may make them react with the cement alkali. As the adhesion of aggregate grains with the hydrated cement grout weakens, individual grains gradually chip away from the surface from the usable flooring surface.
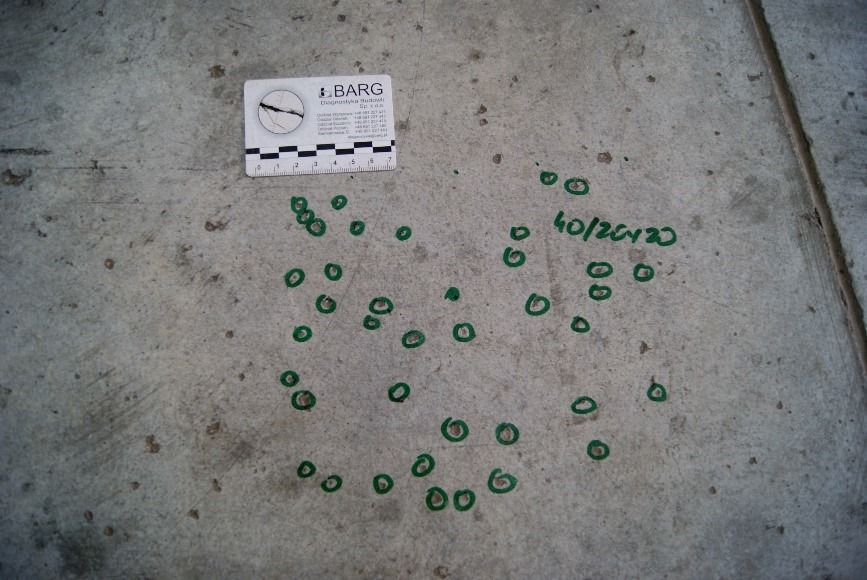
Chipping Away Grains of the Dry-Shake
The pattern of the chip formation in the flooring is related to the projecting part of the grains above the surface of the flooring and its loosening under the influence of friction of the usable motion [traffic, pedestrians]. Grains, which are moved in cycles, loose and chip from the flooring. This mechanism is a result of grains being not properly fixed in, in most of the cases, the fine aggregate.
Protruding Reinforcement Fibres Scattered on the Surface [Photo 7)
The increased amount of steel fibres released from the dispersed reinforcement from the flooring slab can have many causes. One of the main reasons is the excessive trowelling. A frequent reason for defects is also the phenomenon of so-called bleeding [releasing water onto the surface of the concrete) while making the construction panel, making it difficult to shape and trowel the flooring. Increased amount of water in the near-surface layer of the flooring makes the concrete structure locally weakened, reducing its surface strength and durability through its excessive abrasion as it is used.
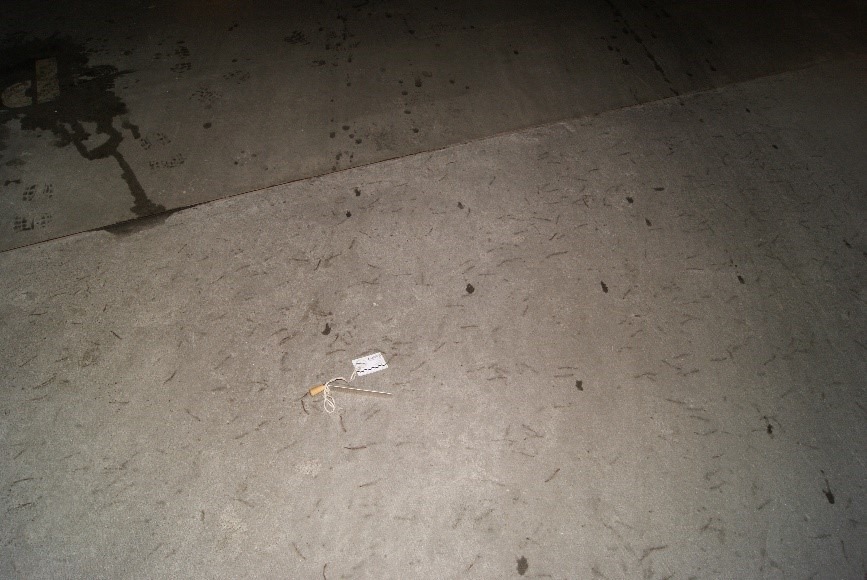
Degraded Concrete Surface Caused by Frost Corrosion [Photo 8)
Heavy frost corrosion or frost corrosion caused by the presence of de-icing salts on the entire surface of the flooring is most often found in floorings exposed to direct atmospheric factors, i.e. located outdoor, in unprotected areas. This is usually caused by failing to adjust the concrete parameters to the prevailing environmental conditions and the making the construction board of concrete that is not resistant to frost in the presence of de-icing salts.

Damage to the Surface due to Acidic Corrosion [Photo 9)
In food production industrial plants, the phenomena of acid corrosion resulting mainly from decomposition of calcium carbonate by acids and leaching erosion as a result of the impact of washing devices can often be found. Mineral surfaces, unlike resin ones, are absorbent. When exposed to chemicals, they do not fully protect against aggressive chemical environment.
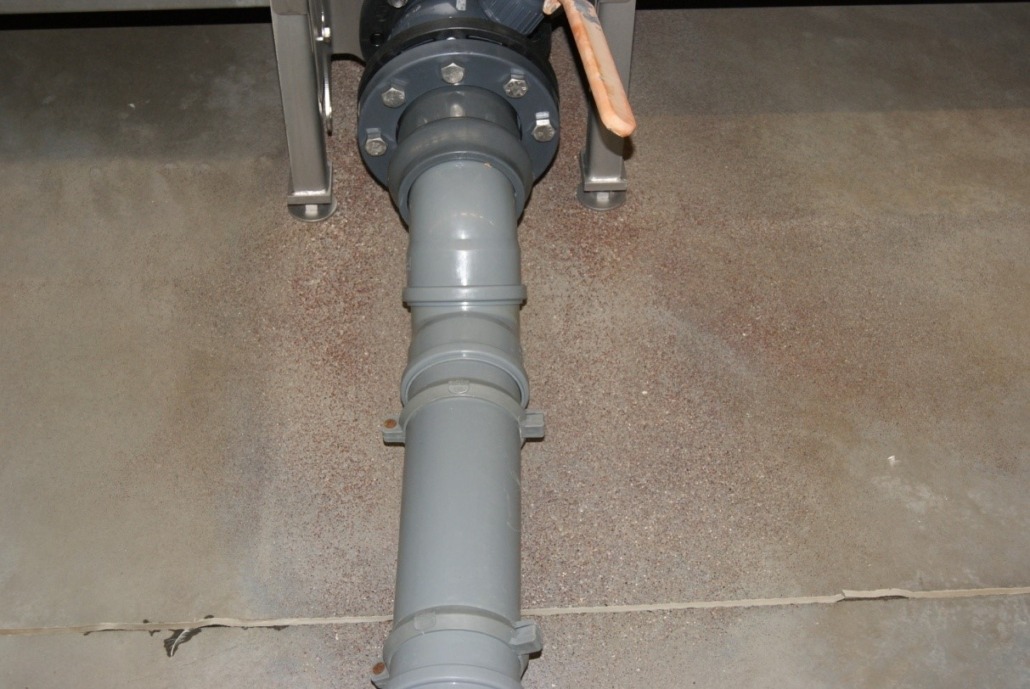
Dry-Shake Top Layer Scaling (Delamination) [Photo 10)
Making industrial floorings in extreme weather conditions often causes many problems with the surface layer scaling. This phenomenon is called horizontal delamination. This is usually resulting from trowelling that may have been begun too late or too early. In addition, water that may have been released as a result of excessive air temperature, too much air flow and insufficient care may affect the scaling. Flooring scaling may reach even 2 cm deep into the surface layer.
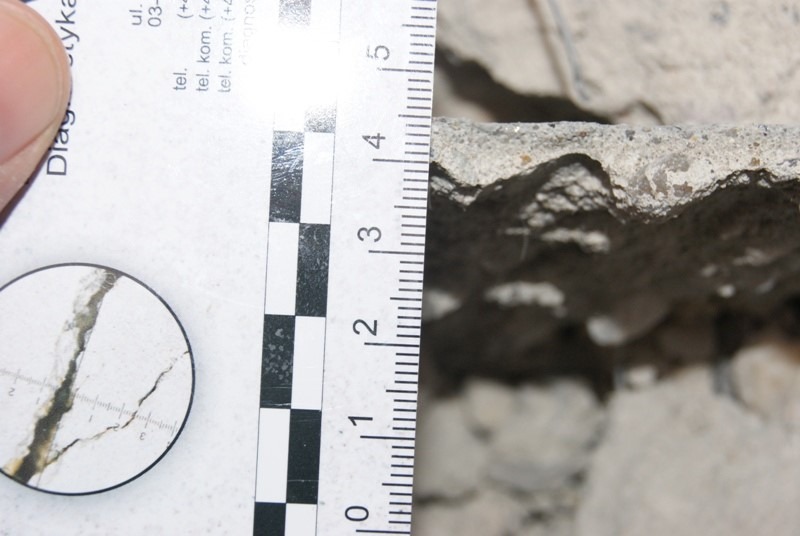
Excessive Abrasibility [Photo 11]
In large-area logistics warehouses, industrial plants or motor vehicle diagnostic stations, since they are heavily used or heavily loaded, the hardening material may be excessively scaled where the vehicles pass. Damage may be the result of wrong selection of the hardening dry-shake with insufficient durability parameters in the prevailing conditions. They are often the result of the wrong care or too small amount of the dry-shake rubbed in.
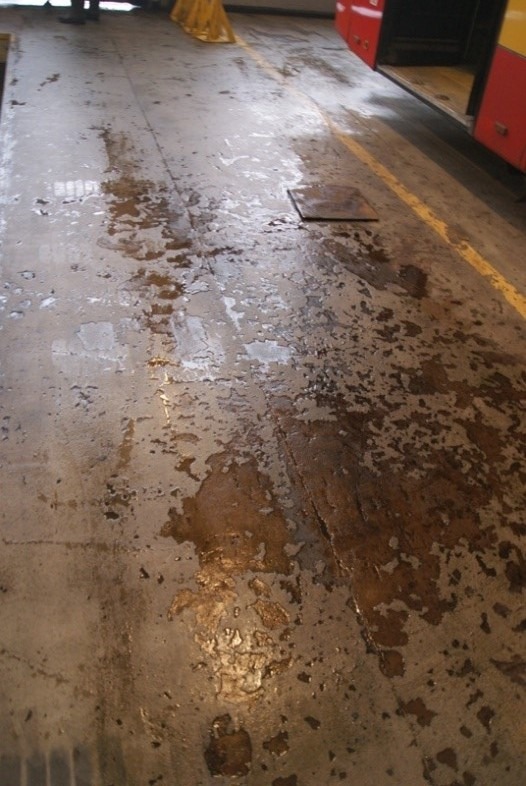
Recapitulation
Industrial floorings with surfaces hardened by the so-called dry-shake are the most popular method of making the finishing layer used nowadays in service and industrial construction industry. At the design stage, physicochemical parameters are often not specified as far as the requirements for floorings are concerned. Most commonly, the designers describe only the strength parameters of concrete in terms of structural layer load. In the design recommendations, often no requirements for the top layer of the flooring are specified or their description is vague. These deficiencies in the designs are the result of failing to properly match the floorings to the real environmental and operational conditions.
Industrial floorings with surfaces hardened by the so-called dry-shake are the most popular method of making the finishing layer used nowadays in service and industrial construction industry. At the design stage, physicochemical parameters are often not specified as far as the requirements for floorings are concerned. Most commonly, the designers describe only the strength parameters of concrete in terms of structural layer load. In the design recommendations, often no requirements for the top layer of the flooring are specified or their description is vague. These deficiencies in the designs are the result of failing to properly match the floorings to the real environmental and operational conditions.
Drawn up by:
Karol Sadłowski, M.Sc.
Damian Urbanowicz, M.Sc.
Maciej Warzocha, M.Sc.
- PN-EN 13318:2002 Floor screeds and materials to make them. Terminology.
- AGI 302. 1R-04; ACI Committee 302, Guide for Concrete Floor and Sfab Construction. America Concrete Institute, 2004.
- Bautech Sp. z o.o., Product Data Sheets.
- PN-EN 206:2014-04 Concrete. Requirements, Properties, Production and Compliance.
- W. Ryżyński, Concrete Floor Surface Hardening, “Construction Engineer”, No. 4/2015.
- B. Chmielewska, G. Adamczewski, Defects and Repairs of Industrial Surface Hardened Floorings, Materials of the XXVI Scientific and Technical Conference “Construction Failures”, 2013.
- H. Rainer Sasse, Design and Performance Requirements, “Industrial floors” Scientific and Technical Seminar, 2007.
- A. Szydło, Road Surfaces Made of Cement Concrete, Polski Cement Sp. z o.o., 2004.
- IBDiM, GDDP, Catalogue of Typical Rigid Surface Constructions. Warszawa 2001.
- DIN 18202 Toleranzen im Hochbau – Bauwerke Tabelle 3.
- PN-EN 12620+A1:2010 Aggregate for Concrete.